三环减速机的设计
4.1引言
三环减速机是在少齿差行星传动的基础上,为了适应现代机械设备对传动装置的要求而诞生的新型减速机。三环减速机由于其原理的独特性,因而对于它的设计也提出了新的适应性要求。本章在前述理论分析的基础上,对三环减速机的设计进行了研究,力求在传动结构和技术参数上,使三环减速机的优越性得以充分实现。
三环减速机的设计包括两个关键部分一少齿差内啮合部分和均载装置部分的设计。对于少齿差内啮合部分,主要是啮合的内、外齿轮变位系数的确定,本章推导了用插齿刀加工的少齿差内啮合变位系数的牛顿迭代公式,较好地解决了这个问题;对于均载装置部分,主要是均载形式的确定和对该种形式的研究,第三章提出一种金属弹性均载环作为三环减速机的均载装置来实现均载和减振,并对均载环进行有限元和动力学分析,验证其具有适宜的刚度、足够的强度、能够满足位移均载的要求;三环减速机属于行星传动装置,因而它的安装也要满足行星传动装配条件,本章将对三环减速机的装配条件进行深入的探讨。本章还对三环减速机的两个关键零件一内齿环板和偏心套进行有限元应力分析,指导进行合理的设计。三环减速机的设计还包括其它一些部分一箱体部分、输入输出轴部分等等,限于篇幅,这些部分在本章中不加以讨论。三环减速机的两个关键零件一内齿环板和偏心套的加工也是不容忽视的问题,由于三片内齿环板必须同时插齿加工且满足180°相位差,因此要求内齿环板工装要有准确的定位;偏心套是三环减速机的薄弱环节,它的制造也应引起足够的重视。限于篇幅,三环减速机的制造在本章中不加以讨论。
4.2三环减速机的设计
4.2.1少齿差内啮合的两个主要限制条件
少断差内啮合传动是指内、外齿轮的齿数差较少的一种行星传动形式,它具有传动比大、体积小、重量轻、加工方便等优点,日益广泛地应用于国防、矿山、冶金、化工、纺织、起重运输、建筑工程、食品工业和仪表制造等部门和行业中。少齿差内啮合传动示意图如图4-1所示。
在设计内啮合齿轮传动时应注意如下几点:
1.为了保证渐开线齿廓,内齿轮的齿顶圆必须大于基圆,即
da2≥db2 (4-1)
三环减速机是在少齿差行星传动的基础上,为了适应现代机械设备对传动装置的要求而诞生的新型减速机。三环减速机由于其原理的独特性,因而对于它的设计也提出了新的适应性要求。本章在前述理论分析的基础上,对三环减速机的设计进行了研究,力求在传动结构和技术参数上,使三环减速机的优越性得以充分实现。
三环减速机的设计包括两个关键部分一少齿差内啮合部分和均载装置部分的设计。对于少齿差内啮合部分,主要是啮合的内、外齿轮变位系数的确定,本章推导了用插齿刀加工的少齿差内啮合变位系数的牛顿迭代公式,较好地解决了这个问题;对于均载装置部分,主要是均载形式的确定和对该种形式的研究,第三章提出一种金属弹性均载环作为三环减速机的均载装置来实现均载和减振,并对均载环进行有限元和动力学分析,验证其具有适宜的刚度、足够的强度、能够满足位移均载的要求;三环减速机属于行星传动装置,因而它的安装也要满足行星传动装配条件,本章将对三环减速机的装配条件进行深入的探讨。本章还对三环减速机的两个关键零件一内齿环板和偏心套进行有限元应力分析,指导进行合理的设计。三环减速机的设计还包括其它一些部分一箱体部分、输入输出轴部分等等,限于篇幅,这些部分在本章中不加以讨论。三环减速机的两个关键零件一内齿环板和偏心套的加工也是不容忽视的问题,由于三片内齿环板必须同时插齿加工且满足180°相位差,因此要求内齿环板工装要有准确的定位;偏心套是三环减速机的薄弱环节,它的制造也应引起足够的重视。限于篇幅,三环减速机的制造在本章中不加以讨论。
4.2三环减速机的设计
4.2.1少齿差内啮合的两个主要限制条件
少断差内啮合传动是指内、外齿轮的齿数差较少的一种行星传动形式,它具有传动比大、体积小、重量轻、加工方便等优点,日益广泛地应用于国防、矿山、冶金、化工、纺织、起重运输、建筑工程、食品工业和仪表制造等部门和行业中。少齿差内啮合传动示意图如图4-1所示。
在设计内啮合齿轮传动时应注意如下几点:
1.为了保证渐开线齿廓,内齿轮的齿顶圆必须大于基圆,即
da2≥db2 (4-1)
2.为了避免轮齿的磨损,内齿轮的齿顶不得变尖,齿顶厚度必须大于(025~0.4)m,即:Sa2>(0.25~0.4)m
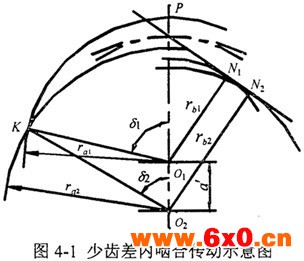
3.切制内齿轮时必须避免范成顶切和径向切入顶切现象
4.必须保证内啮合齿轮副的重合度ε>1。即

5.必须保证不产生齿顶干涉和齿廓重迭干涉,应使GS>O。即

少齿差内啮合传动由于内、外齿轮的齿数差少,易于产生各种干涉。在设计和实际使用中只需满足以下两个主要限制条件:
1.按啮合中心距a′装配时,保证齿轮副不产生齿廓重迭干涉;即应满足齿廓不重迭干涉系数GS>
。
2.保证获得足够的重合度,即应使齿轮副的重合度εa>
。
其中
,
分别为设计要求的少齿差内啮合的重合度和齿廓不重迭干涉系数。
4.2.2少齿差内啮合变位系数的确定
在少齿差内啮合传动中,目前使用最广泛的行星齿轮和中心齿轮的加工方法是范成法。外齿轮大都采用螺旋形的齿轮滚刀在Y8型或Y312型滚齿机上切制而成。内齿轮通常是采用插齿刀在Y54型或Y58型插齿机上插制而成。
1.按啮合中心距a′装配时,保证齿轮副不产生齿廓重迭干涉;即应满足齿廓不重迭干涉系数GS>
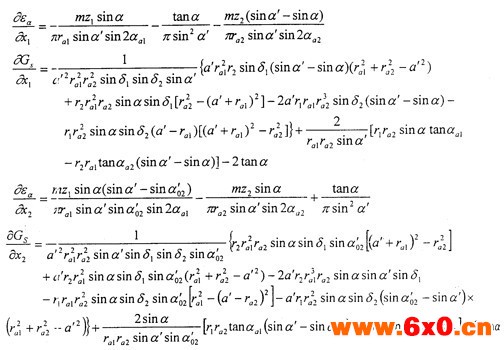
2.保证获得足够的重合度,即应使齿轮副的重合度εa>

其中


4.2.2少齿差内啮合变位系数的确定
在少齿差内啮合传动中,目前使用最广泛的行星齿轮和中心齿轮的加工方法是范成法。外齿轮大都采用螺旋形的齿轮滚刀在Y8型或Y312型滚齿机上切制而成。内齿轮通常是采用插齿刀在Y54型或Y58型插齿机上插制而成。
变位系数的确定是少齿差内啮合传动设计的关键。文献中所述的内、外齿轮都按滚齿加工的计算公式推导出的变位系数的迭代公式,与内齿轮插齿、外齿轮滚齿的实际加工情况不一致,虽然能够保证给定的重合度和齿廓不重迭干涉系数的要求,但是不能保证标准顶隙,而且一般得出的啮合角也比较大。本章推导了少齿差内啮合传动实际加工情况的变位系数的迭代公式,解决了上述问题。
少齿差内啮合传动的两个主要限制条件是否满足,取决于齿轮的有关参数,这些参数包括齿数z0,z1,z2、齿形角a、齿顶高系数
,
、顶隙系数c*、变位系数x0,x1,x2等。由内啮合齿轮副的无齿侧间隙啮合方程:



式中 a——齿形角,一般取a=20°;
a′——啮合角;
z1、z2——分别为外、内齿轮的齿数;
x1、x2——分别为外、内齿轮的径向变位系数。
可得:在z1、z2和a一定时,变位系数xl和x2的变化直接影响到啮合角a′的大小,啮合角是变位系数的函数;而选择变位系数xl、x2的问题,实质上是决定内啮一合齿轮副是否能够消除干涉现象。对于一对啮合齿轮,可把变位系数视为自变量,而把其余的参数作为常量,即限制条件是变位系数的函数。因此,满足两个主要限制条件的问题便归结为求合适的变位系数的问题。
某项限制条件,可以曲线的形式表示在xl,x2坐标系内,若把每个限制条件都以曲线形式绘于x1,x2
某项限制条件,可以曲线的形式表示在xl,x2坐标系内,若把每个限制条件都以曲线形式绘于x1,x2
坐标系内,则它们的交点A便对应着这对齿轮的变位系数,如图4-2所示。
由于限制条件中有许多是超越方程,直接求解变位系数非常困难或是不能求解。因此,本文将讨论如何用逐步逼近的迭代方法来求得同时满足两个主要限制条件的变位系数x1和x2。
由于限制条件中有许多是超越方程,直接求解变位系数非常困难或是不能求解。因此,本文将讨论如何用逐步逼近的迭代方法来求得同时满足两个主要限制条件的变位系数x1和x2。

少齿差内内啮合的重合度计算公式为:

把变位系数x1,x2取作独立变量,把啮合角a′取作中间变量,用牛顿法求解。其迭代程序为:
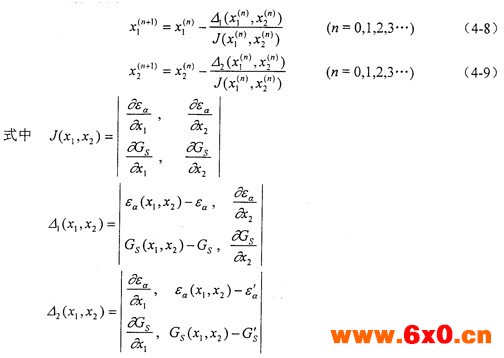
其中
,
分别为设计要求的少齿差内啮合的重合度和齿廓不重迭干涉系数。


应用上述公式迭代时,参考机械工程手册,只要初始值(
)选取得接近精确解(x1,x2),迭代过程就会收敛。

外齿轮的齿顶圆半径:

式中 z0,x0——插齿刀的齿数、变位系数;
da0——插齿刀z0的齿顶圆直径,da0=m(z0+2
+2x0);



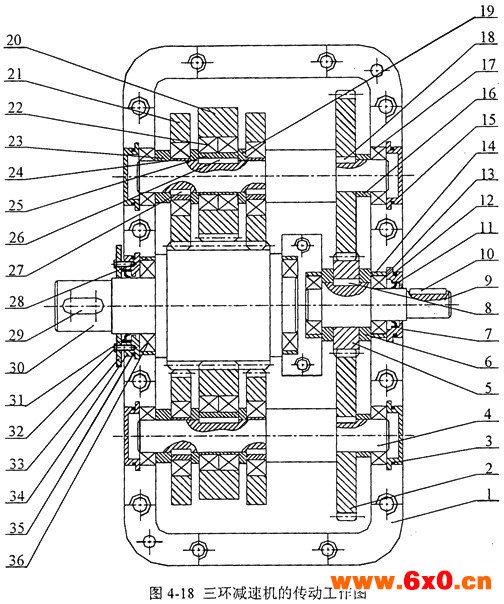
借助于Mathenatica软件,推导出行列式元素为:
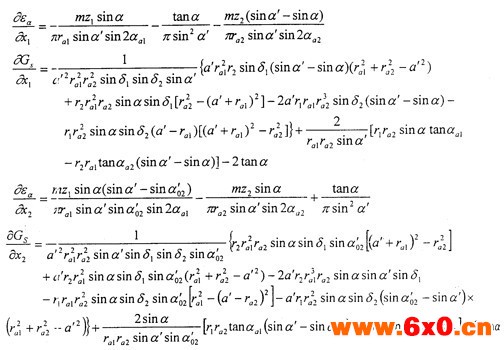
按照迭代过程求得的x1,x2是否满足设计要求,尚需检验变位外齿轮的齿顶厚系数,验算如下:
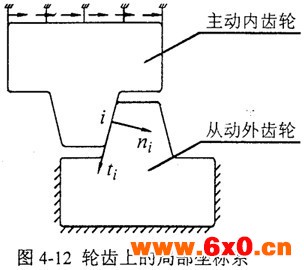
式中
——设计要求的最小的外齿轮的齿顶厚系数。

根据上述公式推导,编制了迭代计算程序,程序框图如图4-3所示。
对于本文的实验样机HITSH145,内啮合齿轮副的参数为:z1=42,z2=44,m=3.5,
=0.8,
=1.1,c*=0.3,a=20°,z0=22,x0=0.126,则可应用上述迭代公式求得当取
≈1.05及
≈0.05时的外、内齿轮变位系数x1和x2。




按照文献中所述的内、外齿轮都按滚齿刀计算的迭代公式,最后得到的计算结果如下所示:
x1=1.433 x2=1.722
′
=38.192° εa=1.05

GS=0. 05 c=1.377mm
a=4.185mm
并且验算外齿轮齿顶厚系数得:

给定初值x1=1.0、x2=1.5,迭代过程及迭代结果如表4-1所示。
按照本文所述的内齿轮为插齿、外齿轮为滚齿的加工方法的迭代公式,最后得到计算结果如下所示:
x1=1.142 x2=1.407

GS=0. 05 c=c*m=1.05mm
a=4.138mm
并且验算外齿轮齿顶厚系数得:

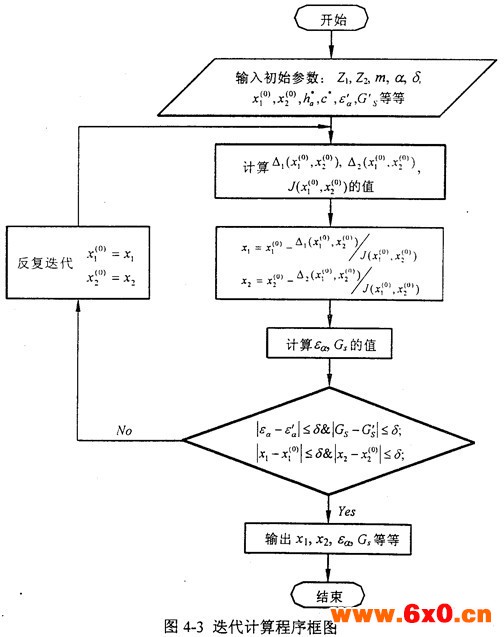
给定初值x1=1.0、x2=2.0,迭代过程及迭代结果如表4-2所示,给定限制条件下的变位系数选择如图4-4所示,交点A便对应着这对齿轮的变位系数x11.14204,x2=1.40742。
表4-1 按滚齿刀计算的迭代过程及迭代结果
迭代次数
第一次
第二次
第三次
第四次
第五次
变
量
x1
1.64556
1.43467
1.43340
1.43339
1.43339
x2
1.89802
1.72276
1.72248
1.72247
1.72247
迭
代
结
果
εa
0.999404
1.037740
1.050295
1.05
1.05
GS
0.610248
-0.050981
0.046851
0.049992
0.05
c
1.731905mm
1.320847mm
1.375545mm
1.377092mm
1.377092mm
′
43.94741°
36.89975°
38.15867°
38.19207°
38.19207°
1.218750
0.282717
0.544335
0.545879
0.545892
表4-2 按滚齿刀计算的迭代过程及迭代结果
迭代次数
第一次
第二次
第三次
第四次
第五次
第六次
变
量
x1
1.11301
1.14312
1.14215
1.14205
1.14204
1.14204
x2
1.33214
1.40130
1.40740
1.40740
1.40742
1.40742
迭
代
结
果
εa
1.06348
1.06606
1.05024
1.05000
1.05000
1.05
GS
1.45340
-0.08768
-0.03195
0.04880
0.04993
0.05
c
1.05mm
1.05mm
1.05mm
1.05mm
1.05m
1.05mm
′
52.2256°
35.6077°
37.1097°
37.3521°
37.3685°
37.3562°
0.72848
0.878514
0.87514
0.87430
0.87424
0.87423
4.2.3 内齿环板的应力分析
内齿环板是三环减速机的关键传动零件,在该传动机构中实质是一连杆,承受一定的冲击;它又是一内齿轮,是一计算分析比较复杂的零件。其强度性能直接影响整机的运动和动态性能,因此有必要对内齿环板的应力和变形进行数值计算。对内齿环板进行有限元分析,首先应该对三环减速机在传动过程中的受力状况进行分析,建立曲型工况下的内齿环板的有限元计算模型;然后利用I-DEAS求出各模型的应力、变形分布及变化规律,对内齿环板强度状况进行研究。
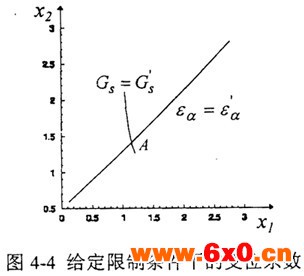
本文研究的HITSH145型三环减速机的内齿环板的结构和受力情况如图4-5所示,孔轴为光孔输入轴,该减速机的主要参数如表4-3所示。Ai孔轴、Bi孔轴为光孔输入轴,O孔为内齿轮,O孔轴为输出轴。每个内齿环板都受到三个力作用:Ai孔与配合轴间的作用力FAi、Bi孔与配合轴间的作用力FBi和O孔处的内齿轮与输出轴上的外齿轮之间的啮合力Fni。
表4-3 内齿环板主要参数表
输入转速nZ
输出扭矩T
齿数Z2
内齿轮模数m
传动比i
齿形角α
压力角α′
966r/min
875N·m
44
3.5mm
21
20°
37.356°
三环减速机的运动和动力通过两根相互平行且各带有三个偏心套的输入轴传递给三片内齿环板,三片环板上的内齿轮同时与输出轴上的外齿轮相啮合,啮合点间的相位差为180°,把运动和动力传递给输出轴。为了考虑三环减速机的惯性力和惯性力偶矩平衡,中间环板的厚度取为两侧环板厚度的两倍。假定两侧环板传递总功率的四分之一,则

根据第二章的三环减速机的受力分析部分和内齿环板的有限元分析要求,可得内齿环板载荷工况如表4-4的上半部所示。在图4-5中,
为Fni,力作用点与x轴正向的夹角,
、
分别为FAi、FBi与x轴正向的夹角。表4-4的下半部列出的是
在12个典型位置时的Fni、FAi、FB。

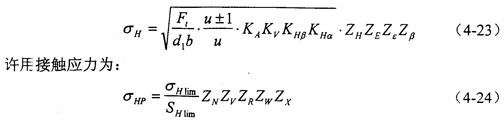


根据内齿环板轴向不能窜动及Ai、Bi孔圆周对称的特点,将约束处理为:圆周Ai、Bi的周边沿轴向(z向)单侧位移为零,内齿轮O无约束。

表4-4 内齿环板载荷工况表
载荷工况编号
1
2
3
4
5
6
7
8
9
10
11
12
集中
力位
置角
(°)
内齿轮
0
30
60
90
120
150
180
210
240
270
300
330
左孔
67.0
86.8
106.5
126.7
148.4
173.4
207.1
259.8
318. 3
356.9
23.0
46.4
右孔
29.1
80.2
136.4
175.1
202.7
225.6
246.6
226.7
286.8
307.4
329.5
355.1
集
中
力
F
(N)
内齿轮O
Fmx
-2403
-2998
-2790
-1834
-387
1164
2403
2998
2790
1834
387
-1164
Fmv
-1834
-387
1164
2403
2998
2790
1834
387
-1164
-2403
-2998
-2790
左孔Ai
FAi
2145
2236
2190
2010
1714
1335
941
697
832
1203
1597
1925
右孔Bi
FBi
959
735
858
1206
1582
1897
2110
2198
2153
1980
1694
1331
根据三环减速机内齿环板的实际结构,设置单元类型、大小及材料特性,内齿环板的分析属于空间问题,选取四面体单元进行计算,选取单元长度为3mm,由Meshing模块共生成实体线性的四面体单元11658个,节点12170个,内齿环板的有限元网格如图4-6所示。12种载荷工况下各模型的约束处理都是相同的,由此建立了内齿环板在12个典型啮合位置时的有限元分析模型。建立约束集和解集,利用I-DEAS软件Model Solution模块对建立的12个有限元模型分别求解,可求出12种载荷工况下各模型的位移及应力如表4-5所示。12种载荷工况下内齿环板的最大位移如图4-7所示,12种载荷工况下内齿环板的最大应力如图4-8所示。

表4-5 内齿环板12种典型工况下的位移及应力计算结果
模型编号
1
2
3
4
5
6
7
8
9
10
11
12
位移δ
10-3mm
全
局
值
Max
16.4
2.83
3.47
7.64
7.75
2.37
1.74
2.81
3.34
8.19
7.73
2.57
应力值
σMPa
Max
13.5
9.36
14.8
12.3
13.9
9.97
15.0
10.0
11.3
13.1
13.5
10.5
Min
×10-2
1.09
1.81
2.61
1.76
1.79
2.32
6.72
1.44
3.27
1.88
3.68
1.33
由图4-7、4-8可知,内齿环板的应力与位移都以360°为周期变化,最大位移出现在 =270°时的工况位置,这是因为此时的啮合力Fni和Bi孔与配合轴间的作用力FBi都出现在
=270°附近,它们的弯曲效应和剪切效应共同作用,出现位移的最大值点,同时也说明环板的最上部、最下部是环板位移的瓶颈环节;最大应力出现在180°+α′时的工况位置,这是因为此时的啮合力Fni、Ai孔与配合轴间的作用力FAi和Bi孔与配合轴间的作用力FBi都出现在
=180°附近,它们的弯滋效应和剪切效应共同作用,出现应力的最大值点,同时也说明环板内齿轮与两个Ai孔、Bi孔的联接部分是内齿环板应力的瓶颈环节。
4.2.4偏心套的有限元分析
在三环减速机中,高速输入轴上要加工三对偏心轴颈,依次安装三个环板。由于中间一块环板的安装比较困难,一般采用图4-9所示的偏心套结构,高速轴1与偏心套2、3、4之间通过平键联接,轴与偏心套之间为过渡配合H7/k6,而偏心套通过环板轴承5与环板相联。
偏心套是高速输入轴上的主要传递扭矩部件,由第二章分析可得,偏心距e=4.18mm,由于偏心结构和装配位置上的限制,所以它成了三环减速机中的薄弱环节,有必要对其进行深入的分析。
在三环减速机中,高速输入轴上要加工三对偏心轴颈,依次安装三个环板。由于中间一块环板的安装比较困难,一般采用图4-9所示的偏心套结构,高速轴1与偏心套2、3、4之间通过平键联接,轴与偏心套之间为过渡配合H7/k6,而偏心套通过环板轴承5与环板相联。
偏心套是高速输入轴上的主要传递扭矩部件,由第二章分析可得,偏心距e=4.18mm,由于偏心结构和装配位置上的限制,所以它成了三环减速机中的薄弱环节,有必要对其进行深入的分析。
对于偏心套来说,首先计算它的受力情况;假定中间环板的偏心套所受载荷为两侧环板的2倍,其它环板平均分配载荷。在额定输出扭矩T2=875N.m下,偏心套承受的扭矩为:
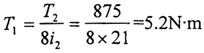
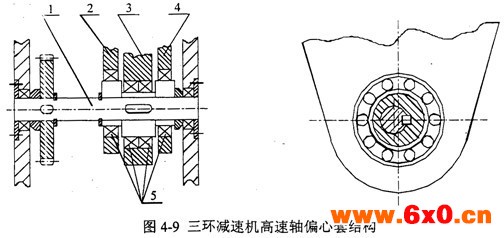
应用I-DEAS软件,按照空间问题求解,根据如图4-10所示的偏心套的结构,设置单元类型为四面体、单元长度为3mm及材料特性为45号钢,由Meshing模块共生成四面体单元3988个,节点1042个,它的有限元分析模型如图4-11所示,由于是平键联接,所以载荷均匀地作用在偏心套主动键槽一侧;由于偏心套可以转动。则边界条件取为偏心套内、外两个圆柱面z向旋转自由。建立约束集和解集,运用Model Solution模块求得结果如下:
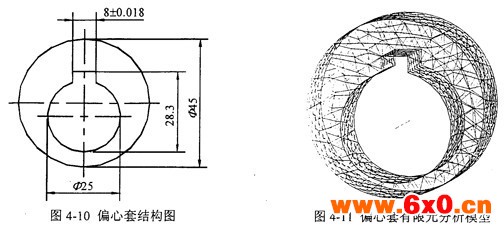
此时偏心套的位移ε为:
εmin=0;
εmax=l.43E-02mm,发生在键槽主动侧边。
此时偏心套的应力σ为:
σmin=2.38E一02MPa;
σmax=5.13E+01MPa,发生在键槽主动侧边。
偏心套的材料为45号钢,由机械工程手册第一卷查得:45号钢的抗拉强度σb≥3.35E+02MPa,远远大于σmax,所以足够满足强度要求,所以偏心套在工作状况下是安全的。
εmin=0;
εmax=l.43E-02mm,发生在键槽主动侧边。
此时偏心套的应力σ为:
σmin=2.38E一02MPa;
σmax=5.13E+01MPa,发生在键槽主动侧边。
偏心套的材料为45号钢,由机械工程手册第一卷查得:45号钢的抗拉强度σb≥3.35E+02MPa,远远大于σmax,所以足够满足强度要求,所以偏心套在工作状况下是安全的。
4.2.5三环减速机多齿啮合的研究
三环减速机的内齿环板和外齿轮构成内啮合齿轮副,是三环传动的核心所庄。对于齿数差较多的内齿轮副,其重合度有足够大的数值。而对于齿数差很小的内齿轮副,由于采用了短齿或超短齿以及较大的啮合角,因此其重合度急剧下降。无论是以传递动力为主要目的,还是以传递运动为主要目的,为了保待齿轮传动的连续性,理论上重合度应大于1。在少齿差内齿轮副中,由于相邻的若干对轮齿之间的齿廓间距十分靠近,在运转时因变形而成为多对齿接触,提高了少齿差传动的承载能力。
对于由主动轮和从动轮组成的齿轮副除满足弹性力学的一般方程外,在齿面啮合点法向上满足位移非嵌入条件,在切向方向满足库仑摩擦定律。只要主动轮输入转矩一定,根据轮齿啮合面的接触状态,其啮合面可以分为三种边界状态。对于由主动轮和从动轮组成的接触问题,可将其分成两个独立的物体,对主动轮和从动轮分别建立在整体坐标系下的有限元基本方程:
三环减速机的内齿环板和外齿轮构成内啮合齿轮副,是三环传动的核心所庄。对于齿数差较多的内齿轮副,其重合度有足够大的数值。而对于齿数差很小的内齿轮副,由于采用了短齿或超短齿以及较大的啮合角,因此其重合度急剧下降。无论是以传递动力为主要目的,还是以传递运动为主要目的,为了保待齿轮传动的连续性,理论上重合度应大于1。在少齿差内齿轮副中,由于相邻的若干对轮齿之间的齿廓间距十分靠近,在运转时因变形而成为多对齿接触,提高了少齿差传动的承载能力。
对于由主动轮和从动轮组成的齿轮副除满足弹性力学的一般方程外,在齿面啮合点法向上满足位移非嵌入条件,在切向方向满足库仑摩擦定律。只要主动轮输入转矩一定,根据轮齿啮合面的接触状态,其啮合面可以分为三种边界状态。对于由主动轮和从动轮组成的接触问题,可将其分成两个独立的物体,对主动轮和从动轮分别建立在整体坐标系下的有限元基本方程:
[KI]{UI}={PI}+{RI} (4-14)
[KII]{UII}={PII}+{RII} (4-15)
式中 [KI],[KII]——主动轮、从动轮的刚度矩阵;
{UI},{UII}——主动轮、从动轮的节点位移向量;
{PI},{PII}——作用于主动轮、从动轮的外载荷向量;
{RI},{RII}——接触力向量。
用rij和uij分别表示轮齿在第i个接触点局问坐标系j(j=n,t)方向上的接触力分量和位移分量,局部坐标系如图4-12所示,上标(1)、(2)分别表示主动内齿轮和从动外齿轮,则
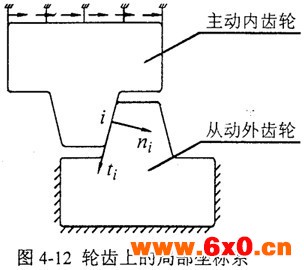
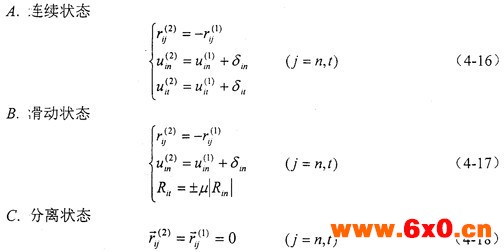
式中 μ——齿面摩擦系数;
δin——齿面接触点i在法向方向的初始间隙;
δit——齿面接触点i在切向方向的初始间隙。
由齿面不同接触状态及轮齿接触的总刚度矩阵得到齿轮啮合面的柔度矩阵方程为:
[fi]{
}={δi}-{△pi}(4-19)

式中[fi]——啮合面接触点的柔度矩阵;
△pi}——外载荷产生的相对位移矢量;
在I-DEAS软件建模模块中,已经给出一个变量u,它的缺省取值范围为u∈(0,1),根据压力角的实际取值范围,可以将其设为u=tanαi,则轮齿渐开线的参数方程可以写成:
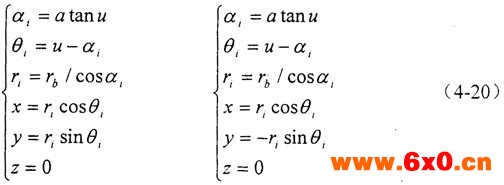
式中 rb——齿轮基圆半径;
上式参数方程则给出了两支以点(rb,0)为基圆上起点的渐开线。实际上,我们希望得到上述参数方程所描述的两支渐开线被齿根圆和齿顶圆所截得一部分。根据已确定的齿轮参数,经过齿根圆和齿顶圆截断(Trim)、绕分度圆圆心旋转(Rotate)和绕分度圆圆心阵列(Array),然后画出中心圆,便得到齿轮的平面模型。经过拉伸深度为齿轮宽度的拉伸(Extrude),便得到齿轮的动态模型。表4-6所示为齿轮建模过程中的参数。
表4-6齿轮建模参数
项目
类别
分度圆 分度圆弧 分度圆齿厚 分度圆上两支渐开线 渐开线需旋
直径 齿厚 所对中心角 所对中心角 转角度
变位外齿轮
变位内齿轮
147mm 8.4073652mm 6.55383° 1.708561° 4.131190°
154mm 1.913O44mm 1.423498° 1.708564° -0.142533°
根据内、外齿轮啮合时的几何位置分别计算出各接触齿对的初始间隙,各接触齿对的初始间隙如表4-7所示。由三环减速机传动可知,内齿轮为主动轮,外齿轮为从动轮,因此边界条件处理为约束内齿轮副的径向方向和约束外齿轮副周边,载荷转矩施加在内齿轮切线方向上。接触齿对的有限元模型如图4-13所示。根据内、外齿轮的结构,设置单元类型、大小及材料特性,轮齿啮合属于平面应力问题,选取四节点单元进行分析计算,四节点单元节点厚度取为相应的内、外齿轮厚度。由Meshing模块共生成四边形单元10503个,节点11066个,运用I-DEAS软件,根据前述的误差分析,采用间隙单元法,建立约束集和解集,运用Model Soltion模块求得结果。
表4-7 内外轮齿齿廓间的最小间隙 (mm)
齿对号
5-5 4-4 3-3 2-2 1-1 2′-2′ 3′-3′ 4′-4′ 5′-5′
间隙
0.042 0.021 0.015 0.008 0 0.008 0.015 0.021 0.042
经过间隙单元法迭代计算,得到啮合过程中,由于轮齿的变形而形成了多齿接触。图4-14所示为由于轮齿的变形,形成了5个齿的接触,以及载荷在轮齿之间的分配比例。当有5个齿参与啮合时,最大主应力为73MPa;假定内、外齿轮的1号齿在齿面上b点相互接触,图4-15所示为轮齿接触时,外齿轮上载荷最大的轮齿1号面的齿面载荷分布情况:图4-16所示为轮齿接触时,内齿轮上载荷最大的轮齿1号面的齿面载荷分布情况。

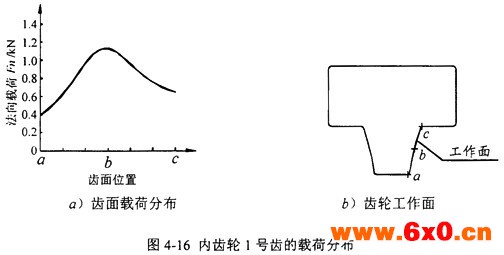
4.2.6三环减速机强度的校核
三环减速机二级传动属于少齿差传动,少齿差传动轮齿工作面上的接触强度不是其在承载能力上的薄弱环节,尤其是轮齿工作表面上的疲劳点蚀破坏未见发生过。一般不进行其齿面接触强度校核,而只进行其齿根弯曲强度校核。区为少齿差传动的g-b齿轮副为内啮合齿廓的相互接触,其齿廓曲率中心位于同一方向,而且两曲率半径p1和p2的值较为接近。因此,其轮齿承载后所产生区接触应力较小。
对于本文提出的三环减速机来说,它的传动参数如表4-8所示:
对于本文提出的三环减速机来说,它的传动参数如表4-8所示:
表4-8三环减速机的传动参数
一级传动比i1
二级传动比i2
总传动比i=i1·i2
输入转速n
输出扭矩T
35/23
21
735/23
1440r/min
875N·m
本文中的三环减速机的第二级传动参数如表4-9所示:
表4-9 第二级传动参数
内齿轮齿数Z2
外齿轮齿数Z1
模数mn
啮合角α′
齿形角α
44
42
3.5mm
37.356°
20°
由于三环传动同时啮合的齿数多,由前述的分析可知,在传动中共有五个齿参与啮合,因此至少可按两齿均匀受力来校核齿根弯曲强度。因采用30°切线法求齿形系数,故这种计算方法是极其粗略的,在下面章节还将进行比较精确的有限元分析。
对于本文的三环减速机,假定载荷分布均匀,本章只校核一块两侧环板和外齿轮的齿根弯曲强度。每一块两侧环板承受扭矩 T,环板宽度b=19mm,外齿轮承受扭矩T,齿宽b=86mm。则计算齿根弯曲应力为:
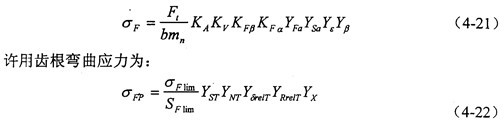
式中 各系数的意义参见机械工程手册。
根据本文的三环减速机的实际应用情况和结构,环板和外齿轮的材料皆是45号钢质处量,可取σFlim=290N/mm2选取各项系数代入上式,求得弯曲强度如表4-10所示。
表4-10 环板和外齿轮的轮齿弯曲强度 (MPa)
外齿轮许用应力
σFP1
环板轮齿许用应力
σFP2
外齿轮计算应力
σFP3
环板轮齿计算应力
σFP4
424.6
437.3
183.8
204
取最小安全系数SFlin=1.5,由计算结果可知,σFP≥σF,所以环板内齿轮、外齿轮均满足齿根弯曲强度要求。
三环减速机的一级传动是渐开线圆柱齿轮传动,第一级的承载能力取决于接触强度。三环减速机的第一级传动参数如表4-11所示。
表4-11 第一级传动参数
输入齿轮齿数Z3
输入齿轮齿宽b3
输入齿轮齿数Z4
输出齿轮齿宽b4
模数m
齿形角α
46
25mm
70
20mm
2.5mm
20°
校核接触应力,计算接触应力为:
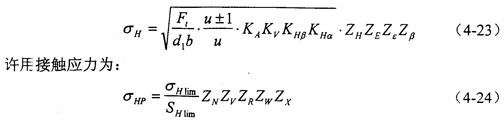
式中各系数的意义参见机械工程手册。
根据本文的三环减速机的实际应用情况和结构,一级传动齿轮的材料皆是45号钢调质处理,可取σHlim=690N/mm2,选取各项系数代入上式,求得接触强度如下:
根据本文的三环减速机的实际应用情况和结构,一级传动齿轮的材料皆是45号钢调质处理,可取σHlim=690N/mm2,选取各项系数代入上式,求得接触强度如下:
σH=319.74N/mm2
σHP=548N/mm2
取最小安全系数SHlim=1.5,由计算结果可知,σHP≥σH,所以,一级传动满足接触强度要求。
4.2.7三环减速机的参数设计
4.2.7三环减速机的参数设计
影响三环减速机传动综合性能的参数很多,其中有传动的中心距ZL、一级定轴传动大、小齿轮参数(模数、齿数、宽度等)、二级少齿差传动齿轮参数(模数、齿数、宽度、变位系数、重合度等)、均载机构参数(均载环形式、结构等)等。三环减谏机几何尺寸及各零部件相对位置如图4-17所示。主要考虑了以下几个方面:
确定三环减速机传动的参数时,
1.在传动性能指标(输出扭矩、传动比、几何尺寸等)上,与重庆专用机械制造公司生产的三齿环减速机SCH145一致,这样可以在同等程度上,比较它们的性能优劣;
2.满足作为行星传动的传力条件、装配条件等;
2.满足作为行星传动的传力条件、装配条件等;
3.一级定轴传动和二级少齿差传动尽可能等强度设计,在保证低速级一二级传动强度的基础上,确定一级传动的参数;
4.选择合理的均载环形式、结构,使均载环具有适宜的刚度、足够的强度;
5.在满足给定的传动功率条件下,使三环减速机具有较小的体积和重量;
6.合理选择各个零部件的结构,使加工制造易于实现;
根据上述原则,对三环减速机进行了设计,其参数如表4-12所示。

表4-12 三环减速机基本参数表
名称
特性
中心距2L
290mm
一级传动小齿轮模数、齿数、宽度
2.5mm、46、25mm
一级传动大齿轮模数、齿数、宽度
2.5mm、70、20mm
二级传动输出齿传输线模数、齿数、宽度、变位系数
3.5mm、42、86mm、1.142
二级传动两侧环板内齿轮模数、齿数、宽度、变位系数
3.5mm、44、19mm、1.407
二级传动中间环板内齿轮模数、齿数、宽度、变位系数
3.5mm、44、38mm、1.407
二级传动重合度
1.05
二级传动啮合角
37.356°
均载方式
金属弹性环均载
均载环形式
n=4m+4型金属弹性环
4.2.8 三环减速机的结构设计
根据三环减速机传动的基本参数以及这种传动的传递的功率情况,进一步对三环减速机传动进行结构设计。表4-13所示为三环减速机结构参数。
表4-13 三环减速机的结构参数表
名称
特性
偏心套外圆直径
ф45mm
偏心套偏心距
4.18mm
一级输入轴轴承型号
左端NU204/P6,右端NU204/P6
偏心轴轴承型号
左端NU205/P5,右端NU205/P5
二级输出轴轴承型号
左端6211,右端6211
环板轴承型号
NU209/P6
均载环结构
ф2mm,内、外圆周各均布八个凸台
箱体结构
焊接、部分式
密封形式
骨架密封圈和O型密封圈密封
润滑方式
油池润滑
根据三环减速机的基本参数和结构参数,设计出三环减速机的传动工作图如图4-18所示。
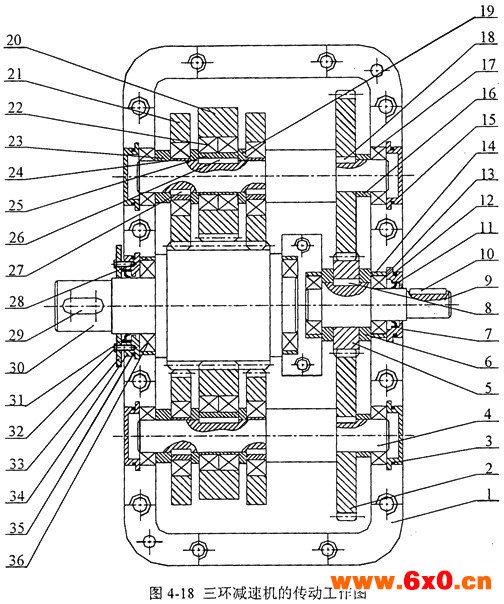
4.2.9三环减速机的效率计算
机械效率η反映了驱动力所作的功在机械中的利用程度,它表示为输出功与输入功的比值。
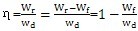
式中 Wr——输出功;
Wd——输入功;
Wf——损耗功。
本文研究的三环减速机是由一级定轴圆柱齿轮传动和二级三环少齿差传动组成,它的效率η由一级传动效率和二级传动效率串联而成,即
η=η1η2 (4-26)
Wd——输入功;
Wf——损耗功。
本文研究的三环减速机是由一级定轴圆柱齿轮传动和二级三环少齿差传动组成,它的效率η由一级传动效率和二级传动效率串联而成,即
η=η1η2 (4-26)
一级定轴轮系机械效率概略计算取η1=0.98。
二级少齿差传动的机械效率η2有理论计算值和实测值两种,而以实测值为评价依据。理论值不可能与实测值相同,但在设计时要进行理论计算。
二级少齿差传动的机械效率η2有理论计算值和实测值两种,而以实测值为评价依据。理论值不可能与实测值相同,但在设计时要进行理论计算。
对于少齿差行星传动的总效率吸,可以认为主要由四部分串联而成,即
η2=ηeηbηwη1ηM (4-27)
式中 ηe——行星机构的啮合效率;
ηb——转臂轴承的效率;
ηw——输出机构的效率;
ηM——液力损失的效率。
由上式可见,少齿差行星传动的总效率是考虑到轮齿啮合损失、轴承摩擦损失、输出机构传动损失和液力损失的效率。
三环减速机传动是一种新型的三相并列少齿差行星传动,没有输出机构,它的每一相传动效率η2参考少齿差传动计算如下:
η2=ηeηbηM (4-28)
1.行星机构的啮合效率ηe
由啮合功率法可以得到:
三环减速机传动是一种新型的三相并列少齿差行星传动,没有输出机构,它的每一相传动效率η2参考少齿差传动计算如下:
η2=ηeηbηM (4-28)
1.行星机构的啮合效率ηe
由啮合功率法可以得到:

式中 ηH——转化机构的啮合效率。
三环传动机构的转化机构为定轴少齿差内齿轮副,对于本文研究的三环减速机,因a′>aa1,节点p在啮合线B1B2外,故转化机构的效率计算如下:
三环传动机构的转化机构为定轴少齿差内齿轮副,对于本文研究的三环减速机,因a′>aa1,节点p在啮合线B1B2外,故转化机构的效率计算如下:

式中fg——啮合过程中齿面的摩擦系数,一般取fg=0.06~0.10。
对于本文的三环减速机,各项数值代入上式得:ηe=0.968。
2.转臂轴承的效率ηb

式中 TB——摩擦力矩;
TH——转臂转矩。
概略计算时可近似地取ηb=0.98~0.995。
TH——转臂转矩。
概略计算时可近似地取ηb=0.98~0.995。
3.液力损失的效率ηM

式中 P-传递的功率,kw;
vH——圆周速度,m/s;
b——浸入油中的齿轮的宽度,mm;
E°——在工作温度下油的恩氏粘度,条件度;
Z∑——啮合齿轮副齿数和。
选取上述参数,计算得ηM=0.95。
综上所述,两级三环减速机的总效率:
η=η1η2 =η1ηeηbηM=0.98×0.968×0.99×0.95==89.2%
vH——圆周速度,m/s;
b——浸入油中的齿轮的宽度,mm;
E°——在工作温度下油的恩氏粘度,条件度;
Z∑——啮合齿轮副齿数和。
选取上述参数,计算得ηM=0.95。
综上所述,两级三环减速机的总效率:
η=η1η2 =η1ηeηbηM=0.98×0.968×0.99×0.95==89.2%
4.2.10三环减速机的装配条件
三环减速机与其它行星传动装置一样,存在一个装配条件的问题。装配条件指的是将三个内齿环板均布地装配在两根高速输入轴上,并使这三个内齿环板与输出外齿轮啮合时,保证啮合的瞬时相位差为180°。
下面来分析它的装配条件,由于本文提出的新型三环减速机环板相互之间的相位差为180°,所以在分析时,可以只分析两块环板的装配情况。图4-19所示为装配条件分析图,在两块环板的偏心所构成的二角内,外齿轮1的齿数为:
下面来分析它的装配条件,由于本文提出的新型三环减速机环板相互之间的相位差为180°,所以在分析时,可以只分析两块环板的装配情况。图4-19所示为装配条件分析图,在两块环板的偏心所构成的二角内,外齿轮1的齿数为:
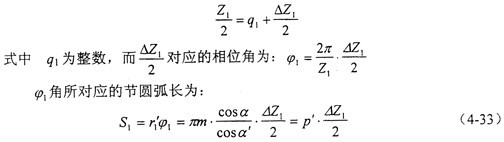
式中P′为节圆齿距。
在两片内齿环板的偏心所构成的π角内,环板上的内齿轮2的齿数为:
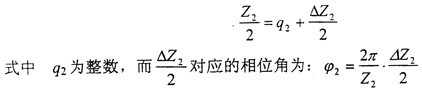


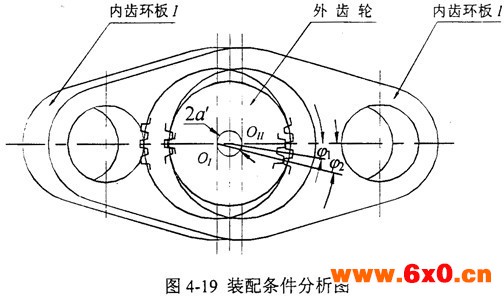

也就是说:当一个内齿环板与外齿轮在某一位置啮合时,另一块环板与外齿轮各自节圆之对滚弧长差为节圆齿距,相对相位差角为内齿轮一个齿所对应的圆心角,此时另一块环板在该位置刚好能够装入。换句话说,对于本文的三环减速机,按照4.3的制造工艺,就可以将三片内齿环板均布地安装在两根高速偏心输入轴上,并且保证它们之间的瞬时相位差呈180°角。
在装配时,将中间环板绕其轴线旋转180°并且翻转,一则保证它们之间的相位差为180°,二则补偿由于加工而引起的偏心误差,进一步提高均载性能。
4.3本章小结
本章在三环减速机力学分析和均载机构研究的基础上,对三环减速机的设计、制造和装配的若干问题进行了深入的探讨和研究
变位系数的确定是少齿差内啮合传动设计的关键。本章在分析少齿差内啮合的两个主要限制条件的基础上,推导了用插齿刀加工的少齿差内啮合变位系数的牛顿迭代公式,不仅满足给定的重合度和齿廓不重迭干涉系数的要求,而且保证标准顶隙,迭代得到的啮合角较小。
内齿环板和偏心套是三环减速机的关键传动零部件,本章应用I-DEAS软件对内齿环板和偏心套进行有限元分析,用来指导结构设计。
对三环减速机的少齿差内啮合多齿啮合问题进行了定量分析,得到啮合齿对间载荷分布规律,对三环减速机的强度校核具有指导意义。
两级三环减速机第一级传动的承载能力取决于接触强度,第二级传动的承载能力取决于齿根弯曲强度。因此对第一级渐开线圆柱齿轮传动进行接触强度校核,对第二级少齿差传动进行齿根弯曲强度校核。
内齿环板是三环减速机传动的关键,本章深入讨论内齿环板的加工制造。
变位系数的确定是少齿差内啮合传动设计的关键。本章在分析少齿差内啮合的两个主要限制条件的基础上,推导了用插齿刀加工的少齿差内啮合变位系数的牛顿迭代公式,不仅满足给定的重合度和齿廓不重迭干涉系数的要求,而且保证标准顶隙,迭代得到的啮合角较小。
内齿环板和偏心套是三环减速机的关键传动零部件,本章应用I-DEAS软件对内齿环板和偏心套进行有限元分析,用来指导结构设计。
对三环减速机的少齿差内啮合多齿啮合问题进行了定量分析,得到啮合齿对间载荷分布规律,对三环减速机的强度校核具有指导意义。
两级三环减速机第一级传动的承载能力取决于接触强度,第二级传动的承载能力取决于齿根弯曲强度。因此对第一级渐开线圆柱齿轮传动进行接触强度校核,对第二级少齿差传动进行齿根弯曲强度校核。
内齿环板是三环减速机传动的关键,本章深入讨论内齿环板的加工制造。
本章对提出的相位差为180°的三环减速机的装配条件作了分析和研究。